本文始于2025年03月,主要讲解流片过程中常见的两种方式,并给出相关优缺点。另涉及相关的专业术语的地方,本文也一并讲解。
1. 芯片流片过程中涉及到的一些专业术语
- 流片(Tapeout)
指芯片设计完成后,将版图数据(GDS格式文件)送至晶圆厂进行制造的过程,也是设计定稿的最后一步。 - 掩膜/光掩膜(Mask/Photomask)
用于光刻工艺中将芯片电路图案转印到晶圆上的光学元件,是实现图案转移的关键工具。 - 晶圆(Wafer)
制造芯片的基本硅片载体,整个芯片的加工和制造均在晶圆上完成。 - 芯片/Die
从晶圆上切割出来的单个电路块,每个die在经过封装后成为最终的芯片产品。 - 切割线/划片线(Scribe Lines/Street)
晶圆上预留用于切割或划分各个芯片(die)之间的区域,确保切割过程的准确性。 - 步进曝光(Step-and-Repeat)
光刻过程中,将晶圆分成多个小区域(shot)逐次曝光的方法,确保整个晶圆均匀获得设计图案。 - Shot
指光刻机一次曝光所覆盖的区域,是实现图案转移的基本曝光单元。 - Seat
在多项目流片或复杂布局中,预先规划并分配给某一设计的固定区域,确保各芯片在晶圆上的位置准确。 - 对准(Alignment)
在光刻和后续工序中,确保各层图案精确重叠的过程,决定了芯片的精度和性能。 - Overlay
指不同曝光层之间的相对位置误差,对准误差直接影响芯片电路的连接和功能实现。 - 工艺节点(Process Node)
指芯片制造中使用的工艺技术节点(如 7nm、28nm 等),代表工艺的先进程度和特性。
这里着重介绍Shot和Seat的概念:
1.1 什么是Shot?
在芯片生产中,“shot”通常指的是光刻机一次性曝光的区域,也称为“曝光单元”或“拍摄区域”。光刻过程并不是一次性将整个晶圆上的图案都曝光出来,而是通过“步进-重复”(step-and-repeat)或“扫描”方式,将光掩膜(或称为“光刻版”)上的电路图案按预定区域分次曝光。下面对“shot”进行解释:
1.1.1 光刻过程中的Shot定义
- 曝光单元:在光刻过程中,晶圆上的一个有限区域通过一次曝光过程得到图案,这个区域就被称为一个“shot”。
- 步进曝光:由于光学系统的物理限制(如镜头视野大小),每次曝光只能覆盖有限的面积,因此需要将晶圆分割为多个曝光单元,然后通过机械步进系统逐个进行曝光。
1.1.2 Shot的技术原理
– 光学投影成像
- 掩膜与光刻机:芯片设计完成后,图案被制作为掩膜。光刻机使用高精度光学投影系统,通过特定波长(如深紫外或极紫外)的光,将掩膜上的图案缩小后投影到覆盖了感光材料(光刻胶)的晶圆上。
- 成像原理:这种投影成像基于光的衍射和干涉原理,利用高数值孔径的镜头系统达到高分辨率成像。单个shot的成像质量直接影响到晶圆上图案的精度和线宽控制。
– 步进-重复机制
- 分区曝光:由于每个曝光镜头只能覆盖一定面积(即shot大小),晶圆需要分为多个区域进行连续曝光。每次曝光后,晶圆通过步进平台精确移动,将未曝光区域移至光刻机的曝光区域内。
- 拼接与对准:多个shot拼接成完整的芯片图案,这就要求每个曝光单元之间的对准精度极高,避免因错位造成电路连接失效或性能下降。
– 工艺参数与限制
- 分辨率限制:单个shot的成像受限于光刻系统的分辨率,分辨率由光源波长、数值孔径及工艺参数决定。随着工艺向更细微的工艺节点发展,shot技术也不断在提高精度和控制误差方面进行优化。
- 曝光均匀性:确保每个shot区域内的光强和成像质量一致,是保证全晶圆图案一致性的关键。系统内的光学均匀性、曝光时间以及光刻胶性能都会对最终效果产生影响。
1.1.3 Shot在芯片生产中的意义
- 生产效率:每个晶圆上需要进行多个shot的曝光,shot数直接影响到生产周期与设备吞吐量。优化shot设计和步进路径可以提高生产效率。
- 技术挑战:随着芯片制程向更细小节点发展,shot间的对准误差、光学衍射效应以及相邻shot边界的拼接问题成为技术难点,促使新一代曝光技术(如极紫外光EUV)的发展。
以上就是芯片生产流程中关于shot的技术原理,从中可以看出,shot不仅是曝光过程中的一个操作单元,更是影响芯片成像质量、生产效率和最终产品性能的重要环节。可参考如下示意图;
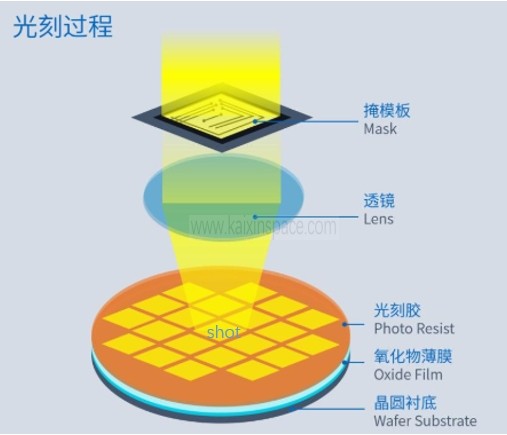
图片来源网络,侵权删!!
1.2 什么是Seats?
在芯片流片生成过程中,“seat”一般指的是在晶圆上预先规划和分配给某个特定设计或芯片的“位置单元”或“座位”。此概念主要体现在多项目晶圆(MPW)或者其他多设计共享晶圆的场景中。下面详细说明“seat”的含义和作用:
1.2.1“Seat”的基本概念
- 定义:
“Seat”可以理解为晶圆上专门预留出来供某一项目或设计使用的区域。类似于为每个芯片分配的“座位”,它标识了该芯片在晶圆布局中的具体位置和范围。 - 作用:
在多设计流片中,每个项目都有自己的seat。这样可以在同一晶圆上同时生产多个设计,同时便于后续的测试、封装和识别。对于设计者和制造厂商来说,seat的确定有助于:- 精确对齐(alignment)
- 确保设计规则(Design Rules)的一致性
- 后续的切割(dicing)和封装流程中正确识别各个芯片位置
1.2.2“Seat”在流片过程中的重要性
- 布局规划:
在流片之前,设计者和晶圆厂需要对整个晶圆进行布局规划。为每个设计分配一个seat,不仅可以高效利用晶圆面积,还能在流片过程中减少因位置偏差带来的风险。 - 对齐和步进曝光:
光刻过程中采用步进-重复(step-and-repeat)技术,每次曝光一个固定区域(shot)。而seat的定义则帮助系统确定每个chip在晶圆上的最终位置,从而保证多个曝光单元拼接成完整图案时的精度和一致性。 - 后续工序匹配:
在晶圆测试、切割和封装过程中,明确的seat分布有助于自动化设备准确识别每个芯片的边界,确保良品率和产品一致性。
1.2.3 切割
- Scribe Lines(切割线):
在各个seat之间,通常会预留切割线(scribe lanes),以便在后续的切割过程中将各个芯片分离。seat的规划需要考虑到这些切割线的宽度和位置。
在芯片流片生成过程中,“seat”概念的引入主要是为了在多项目或复杂晶圆布局中明确每个芯片设计的位置和范围。通过对seat的合理规划,不仅可以提高晶圆利用率,还能确保光刻对齐、后续测试及切割等工艺环节的精准执行,从而提升整体生产效率和产品良率。了解这一概念,对于设计人员和制造工程师来说,都具有重要的指导意义。
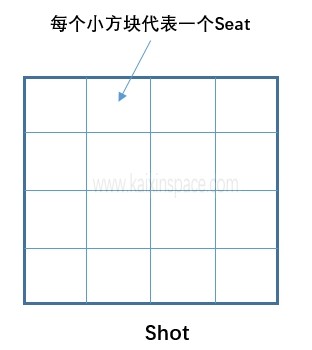
2. MPW(Multi-Project Wafer)
MPW是一种“拼版”流片模式,多个客户的芯片设计共享同一片晶圆,分摊掩模(Photomask)和生产成本。代工厂(如台积电、中芯国际)定期开放MPW服务窗口,客户提交设计文件后,代工厂将其合并到同一套掩模中进行生产。
优点:
- 成本分摊:多个项目共同承担整个晶圆的制造费用,大幅降低单个项目的流片成本。
- 快速验证:适合验证设计功能、工艺兼容性和初步性能,缩短产品研发周期。
- 风险可控:适合原型验证或小批量试产,避免设计错误导致巨额损失。
缺点:
- 设计约束:为满足晶圆上不同项目的工艺要求,通常需要遵守统一的设计规则(Design Rules),这可能限制部分高性能或特殊需求设计的优化空间。
- 后端测试复杂:晶圆上混杂多个项目,测试、拆分和后续封装工作相对复杂。
- 工艺定制性不足:无法针对某一特定设计进行工艺优化,因此在性能和良率上可能不如专用流片来得稳定。
- 产能受限:每个项目在晶圆上分配的面积有限,通常仅支持微小芯片(如5mm²以下)。
- 周期固定:需等待代工厂的MPW排期(通常每季度一次),无法灵活调整时间。
存在这种情况:我们希望把所有die都尽可能的摆在一个Shot里,但由于一个Shot中的各个die的尺寸可能不同,在生产完成后,当进行die切割时,难免会损坏其他die。如下示意图;
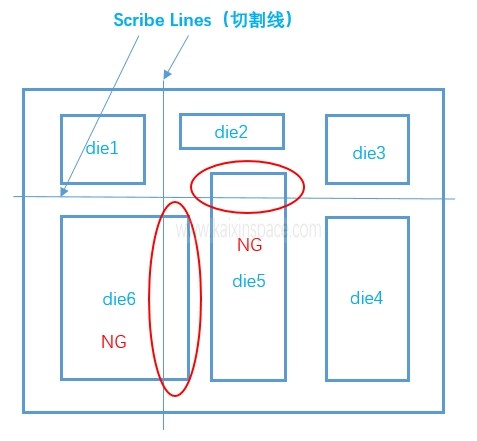
解决的办法:引入”Seats”概念,因为每个seats是有固定的切割路线,可以有效避免切割带来的损坏。
将一个Shot分为多个seats,每个seats按固定面积,不同die的面积按照占用seats个数来划分,多占多分摊成本,少占少分摊成本。比如:每个seats的面积按照2X2计算,当你设计的一颗die面积是3×4时,那你就占用4个seats;如下图所示:A die占用一个seat;B die 占用2个seats; C die占用4个seats; D die则占用8个seats。
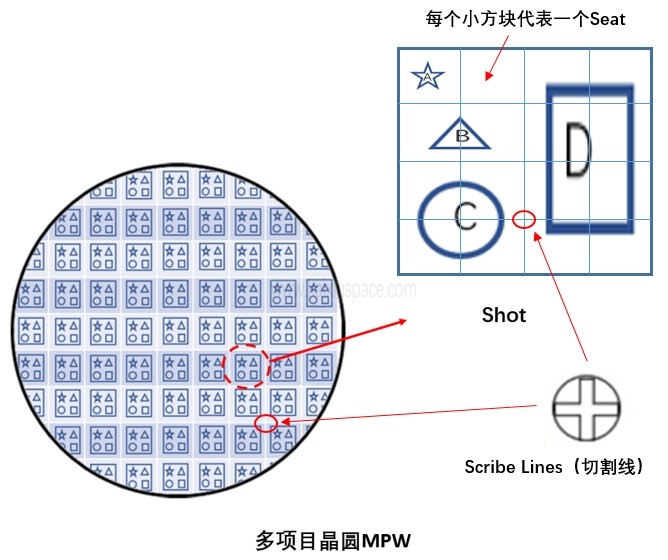
部分图片来源网络,侵权删!!!
3. Full Mask
Full Mask 流片,也称为专用流片,是针对单一芯片设计进行的定制化生产流程。从光掩膜(Photomask)的制作到晶圆的全部加工步骤,均依据该设计专门制定工艺参数和规则。此方式多用于产品进入量产阶段或对性能要求较高的应用场景。
优点:
- 高度定制:工艺流程和掩膜设计可以针对具体芯片进行优化,从而实现更好的电气性能、更低的功耗以及更高的集成度。
- 稳定性好:单一设计专用生产,经过反复工艺验证和优化后,产品良率和性能表现更加稳定。
- 产能自由:支持大规模量产。
缺点:
- 成本高昂:独立制作掩膜组和专用晶圆的费用较高,适合资金充裕或规模化量产的项目。
- 开发周期长:从设计定稿到流片再到量产需要更长时间,且工艺调试和验证流程更复杂。
- 风险集中:由于投入大且流程专用,设计或工艺问题出现时风险较为集中,影响成本和后续改进。
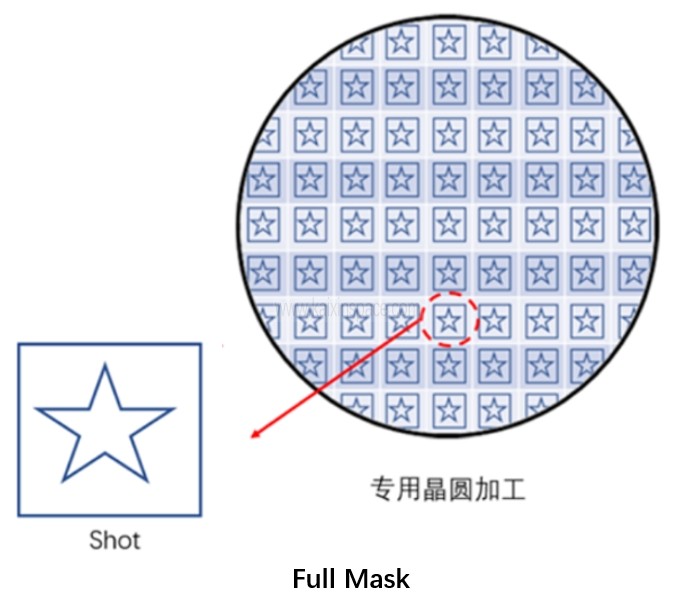
图片来源网络,侵权删!!
4. 总结
一般情况下,公司通常会按照:先MPW验证,然后在到Full Mask量产的流程。
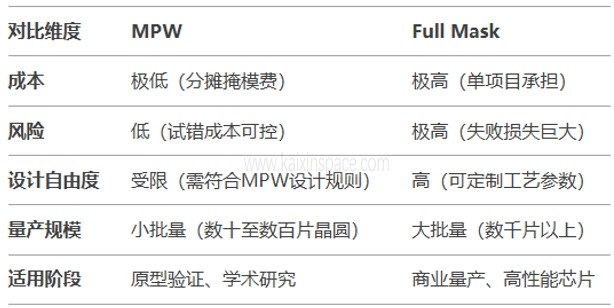